The CNC plasma cutter machine is matched with different working gases (the working gas is the conductive medium of the plasma arc and the heat-carrying body. At the same time, the molten metal in the incision must be removed. The commonly used plasma arc working gases are argon, hydrogen, nitrogen, oxygen, and air. , Water vapor and some mixed gases) can cut all kinds of metals that are difficult to cut by oxygen, especially for non-ferrous metals (stainless steel, carbon steel, aluminum, copper, titanium, nickel). The cutting effect is better. Due to the fast cutting speed and accuracy High, low cost, plasma cutting has been widely used in large industrial CNC applications to small hobbyist shops and is widely used in locomotives, automobiles, pressure vessels, nuclear industry, chemical machinery, general machinery, steel structure, construction machinery and other industries.
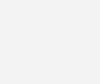
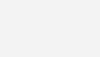
The type of plasma cutter machines
CNC plasma cutter machines are divided into working methods: dry plasma, semi-dry plasma, and underwater plasma; in terms of cutting quality, they are divided into ordinary plasma, fine plasma, laser-like plasma, etc.
The plasma cutting machines provided by our company include flat plasma cutting machine, plate and tube integrated plasma cutting machine, square tube plasma cutting machine, portable plasma cutting machine, round tube plasma cutting machine, gantry plasma cutting machine.
CNC plasma cutter machine, also known as CNC plasma cutting machine, plasma cutter, plasma cutting table, plasma cutting machine.
How to use a plasma cutter ?
Before use and when cutting
- Check and confirm that the power supply, air source, and water source have no leakage, air leakage, or water leakage, and the grounding or zero connection is safe and reliable.
- The trolley and workpiece should be placed in an appropriate position, and the workpiece should be connected to the positive electrode of the cutting circuit, and there should be a slag pit under the cutting working surface.
- The nozzle aperture should be selected according to the material, type, and thickness of the workpiece, and the cutting power, gas flow, and electrode shrinkage should be adjusted.
- The automatic cutting trolley should be run empty and the cutting speed should be selected.
- Operators must wear protective masks, welding gloves, hats, filter dust masks, and soundproof earmuffs. Personnel who do not wear protective glasses are strictly prohibited from directly observing the plasma arc, and bare skin is strictly prohibited from approaching the plasma arc.
- When cutting, the operator should stand upwind to operate. The air can be drawn from the lower part of the workbench, and the open area on the workbench should be reduced.
- When cutting, when the no-load voltage is too high, check the electrical grounding, zero connection, and the insulation of the torch handle. The workbench should be insulated from the ground, or a no-load circuit breaker should be installed in the electrical control system.
- The high-frequency generator should be equipped with a shielding cover, and the high-frequency circuit should be cut off immediately after the high-frequency arc is used.
- The use of thorium and tungsten electrodes should meet the requirements of Article 12.7.8 of jgj33-2001.
Cutting operation and protection of cooperating personnel
- The plasma cutting machine used on site should be equipped with rain, moisture, and sun sheds, and should be equipped with corresponding fire fighting equipment.
- When cutting at high altitude, safety belts must be worn, fire prevention measures should be taken around and below the cutting, and a special person should be supervised.
- When it is necessary to cut pressurized containers, sealed containers, oil drums, pipes, and workpieces stained with flammable gases and solutions, first eliminate the pressure in the containers and pipes, eliminate flammable gases and solutions, and then flush toxic, harmful and flammable Substances; for containers with residual grease, they should be rinsed with steam and alkaline water first, and the lid should be opened to confirm that the container is cleaned, and then filled with water before cutting. Welding in the container should be taken to prevent electric shock and poisoning. And suffocation measures. Air holes should be left in the sealed container, and equipment ventilation equipment should be installed at the inlet and outlet when necessary; the lighting voltage in the container should not exceed 12v, and the welder and the workpiece should be insulated; the special person should be placed outside the container. It is strictly prohibited. Cut inside a container that has been sprayed with paint and plastic.
- It is strictly forbidden to cut pressure vessels and pipelines, live equipment, load-bearing structures, and containers containing flammable and explosive materials under pressure.
- Welding and cutting are not allowed in the open air on rainy days. When working in a humid area, the operator should stand in a place with insulating materials and wear insulating shoes.
- After the operation, the power should be cut off, and the air and water sources should be turned off.
Leave a Reply
You must be logged in to post a comment.