The choice depends on the specific needs and production requirements of the woodworking shop or individual user. Always follow proper safety guidelines and use personal protective equipment when operating panel saws or any woodworking machinery.
The computer beam saw, also the computer panel saw, is a type of panel saw machine combining computer numerical control technology. Different manufacturers may refer it to as panel sizing machine, panel dividing saw, automatic panel sizing saw, or panel sizing center.
It adopts fully automatic computer control and man-machine integration operation. Operators need to input the required data on the touch screen. Then the panel cutting saw runs automatically to accurately cut the panels. With the rapid development of the furniture industry, the precision requirements for panel cutting saw are getting higher and higher.
The disadvantages of manual panel saw machines are becoming more obvious: insufficient precision, chipping, faults, work injuries, low efficiency, etc. The birth of the computer panel table saw for sale has just effectively solved these concerns.
Panel Saw
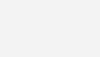
A panel saw is a woodworking machine designed for efficiently and accurately cutting large panels or sheets of wood, plywood, MDF (medium-density fiberboard), and other similar materials. It is especially useful for tasks like cutting large pieces for cabinet making, furniture production, and other woodworking projects.
This machine tool can cut and process all kinds of solid wood panels, wood-based panels, ABS panels, PVC panels, organic glass and other wood structures, and panels with similar hardness. It is one of the necessary equipment for the production of furniture, decoration and other industries.
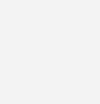
The machine tool is composed of a bed, a mobile worktable, a mobile worktable attached support, a fixed worktable, a main saw, a secondary saw, a transmission lifting mechanism, and a horizontal and vertical guide plate.
The machine tool guide rail is made of aluminum alloy linear guide rail, which is oxidized and has super high wear resistance and no deformation. To ensure that the machine tool can work accurately for a long time, the inclination angle of the main saw blade and the auxiliary saw blade is visually displayed by the precision angle meter, and the operation is very convenient.
Sliding Table Saw
A sliding table saw is a type of woodworking machine used for making straight cuts in wood and other materials. It is characterized by a sliding table that allows the workpiece to be smoothly guided through the cutting blade.The sliding table is the primary feature of a sliding table saw. It provides support and stability for the workpiece while allowing it to slide smoothly and accurately through the blade. The sliding table can be adjusted to different lengths, accommodating various sizes of workpieces.
Besides, it can also make grooves at any angle (e.g. 22.5°, 45°, 90°). This can be realized by adjusting the angle and height of the panel saw machine blade. At the same time, the panel saw machine can also saw all kinds of insulating plates, thin aluminum plates, and aluminum profiles.
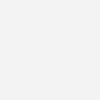
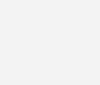
90° Panel saw
It can only cut right angles and is used in the production of panel furniture, cabinets, wardrobes and other construction industries.
45° Panel saw
The saw blade can be tilted, not only can cut right angles, but also can 0°—45° boards for solid wood furniture and soft bags.
key features and benefits of sliding table saw
Sliding Table: The sliding table is the primary feature of a sliding table saw. It provides support and stability for the workpiece while allowing it to slide smoothly and accurately through the blade. The sliding table can be adjusted to different lengths, accommodating various sizes of workpieces.
Increased Cutting Capacity: Sliding table saws typically have a larger cutting capacity compared to traditional table saws. The sliding table allows for longer and wider workpieces to be cut with ease, making them ideal for cutting large panels, sheets, or dimensional lumber.
Precise and Straight Cuts: The sliding table mechanism ensures precise and straight cuts. The workpiece remains stable and straight throughout the cutting process, reducing the risk of errors and improving the overall accuracy of the cuts.
Versatility: Sliding table saws can perform a wide range of cutting tasks. In addition to straight cuts, they can also be used for bevel cuts, miter cuts, and even some joinery operations depending on the available features and accessories.
Safety Features: Sliding table saws often come equipped with safety features such as blade guards, riving knives, and anti-kickback devices. These features help protect the operator from potential accidents and ensure safer operation.
Efficient and Time-Saving: The sliding table mechanism allows for efficient and smooth material handling, reducing the need for manual feeding and improving workflow. This can save time and increase productivity, especially when working with larger or heavier workpieces.
Professional and Industrial Applications: Sliding table saws are commonly used in professional woodworking shops and industrial settings where high-volume and high-precision cutting tasks are performed. They are often favored by cabinetmakers, furniture manufacturers, and other woodworking professionals.
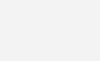
When selecting a panel saw, consider factors such as the size and capacity of the machine, the power and speed of the motor, the available safety features, and the overall build quality. It’s important to choose a panel saw that suits your specific needs and the types of materials you work with.
This machine tool can cut and process all kinds of solid wood panels, wood-based panels, ABS panels, PVC panels, organic glass and other wood structures, and panels with similar hardness. It is one of the necessary equipment for the production of furniture, decoration and other industries.
Sliding panel saw machine is composed of a bed, a mobile worktable, a mobile worktable attached support, a fixed worktable, a main saw, a secondary saw, a transmission lifting mechanism, and a horizontal and vertical guide plate.
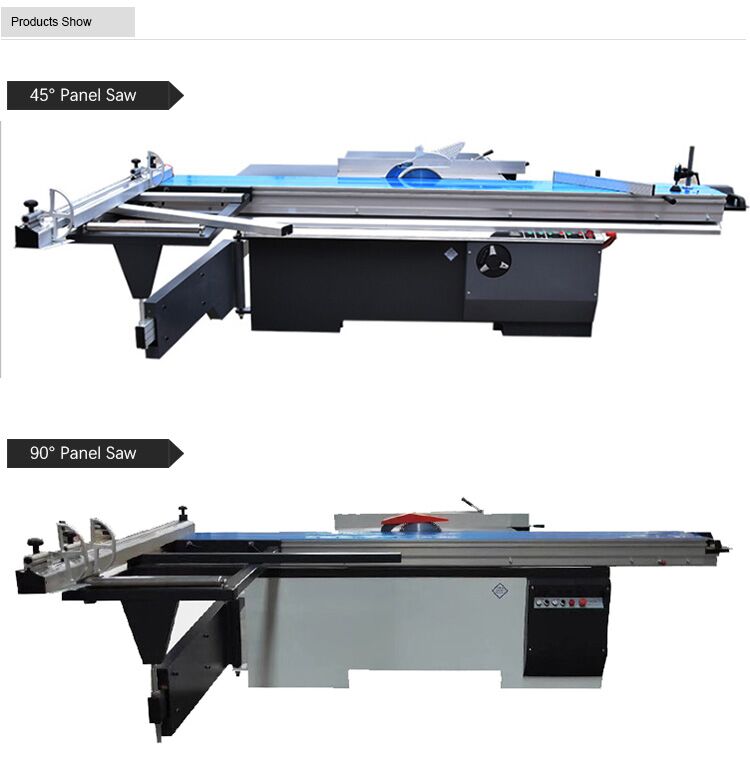
The machine tool guide rail is made of aluminum alloy linear guide rail, which is oxidized and has super high wear resistance and no deformation. To ensure that the machine tool can work accurately for a long time, the inclination angle of the main saw blade and the auxiliary saw blade is visually displayed by the precision angle meter, and the operation is very convenient.
1.Positioning plate 2.Bracket 3.Boom support rod
4.staff gauge 5.Auxiliary support 6.Workbench
7.Main saw blade 8.Auxiliary saw blade
9.Hand saw blade adjustment wheel
10.Backing 11.Control button
12.Enlarge the countertop
13.Auxiliary countertop
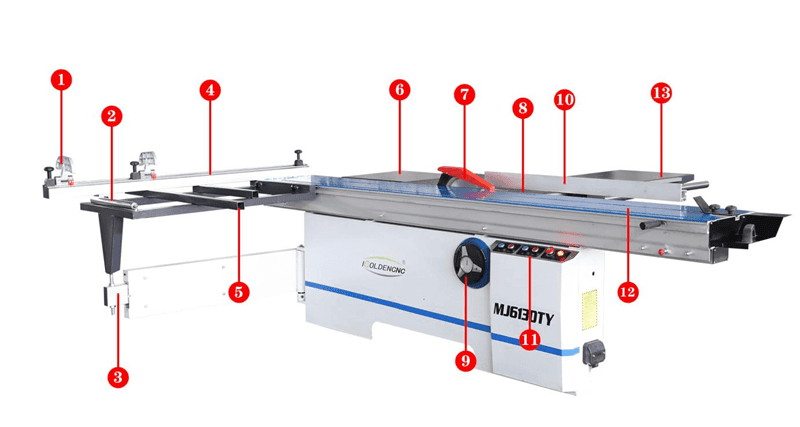
- This machine tool can provide vertical and horizontal sawing of square lumber and panels, and is suitable for processing various panels such as construction, furniture, vehicle and ship manufacturing.
- Features: This machine can saw wood, veneer particleboard, various man-made boards, plastic boards, and aluminum alloy boards. There are two saw blades at the front and back. The front is the pre-cutting saw and the back is the main saw. The two saw blades work at the same time, no planing process after sawing, good smoothness, high accuracy, and no burrs.
- The body has a sliding table and a fixed table. Therefore, the machine can be used for sawing and cutting the sheet size without laying a foundation.
2.Sliding Table Saw Technical Parameter
Maximum cutting length | 2800/3000/3200mm |
Maximum cutting width | 1250mm |
Main saw blade diameter | 250-300mm |
Vice saw blade diameter | 120mm |
Main saw blade speed | 4500-6000rpm |
Vice saw blade speed | 8000rpm |
Main saw motor power | 4kw |
Vice saw motor power | 0.75kw |
Machine size | 3050*3150*900mm |
Weight | 800kg |
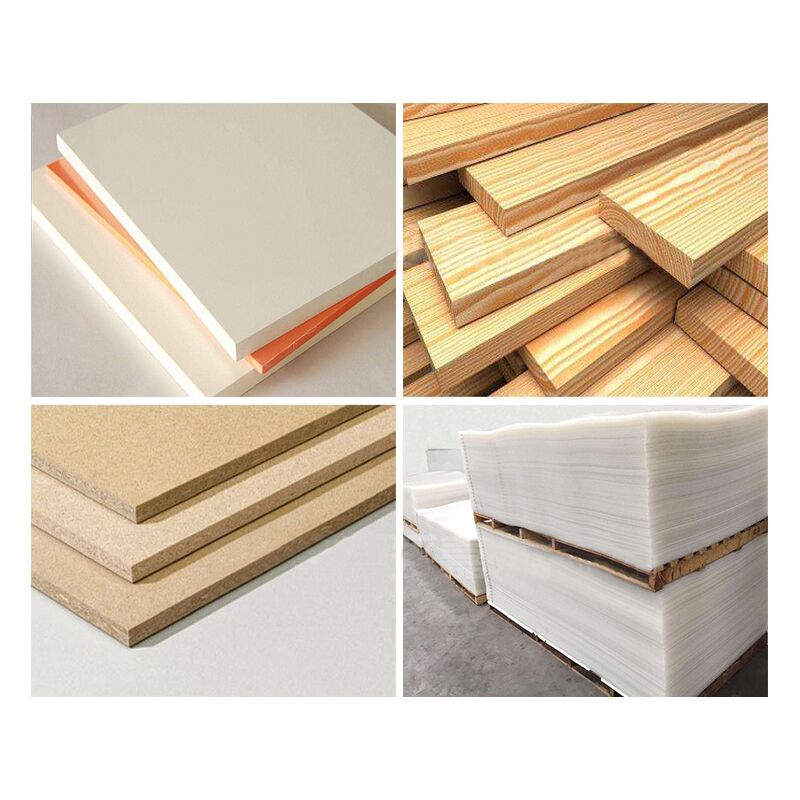
3.Sliding Table Saw Composition and working principle
- The composition of the machine tool: The machine tool is composed of a sliding table part, a fixed table part, a cutting part, and an electrical part.
- 2.Motion system diagram
Working principle: After the adjustment of the machine tool is completed, according to the required plate size, align the backing plate according to the standard size on the worktable. The backing plate can be adjusted horizontally and diagonally. Adjust the main saw blade to an appropriate height (the pre-cutting saw lifting is controlled by the star handle) and then put the plate on the worktable and press the button to realize the cutting.
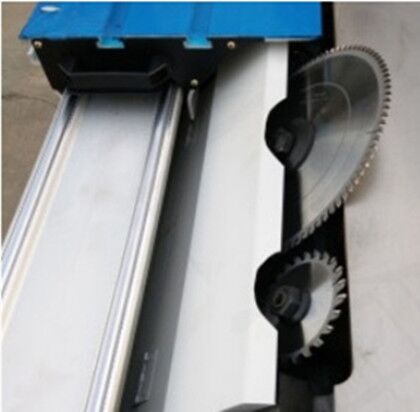
4.Handling, installation, adjustment and trial operation of machine tools
4.1 Handling: When handling the machine tool, avoid shock and vibration. When lifting, pay attention to whether the packaging is tightly bound and whether the lifting point is on the center of gravity of the machine tool. When tilting and rolling, the inclination of the board should not exceed 15°. The diameter of the roller shall not be greater than 60mm. The machine tool should be firmly tied with steel wire rope or hemp rope during lifting. The rope should not be in contact with the protruding part of the machine tool and the exposed processing surface after being tensioned. It must be protected by a replacement or thick paper liner to prevent damage. Paint and finish the surface.
4.2. Installation: The machine does not need to lay the foundation, it can be used after fixing the position.
4.3.Adjustment:
6.3.1Adjustment of the sliding table relative to the saw blade
In order to avoid the second cutting of the teeth when the tool is raised, a free cutting area should be left, that is, the sliding table should not be completely parallel to the saw blade, and the difference in parallelism is 1 meter behind the blade For the maximum 0.1m, for the same reason, the pre-cut saw blade should also have a very small free cutting area.
In order to check the free cutting area, clamp a wooden board on the sliding table. After cutting, stopping and pulling back, it is found that the friction between the wooden board and the saw blade is very small, but the friction is large during sawing, indicating that the machine has been adjusted well. If there is no friction when it is pulled back, but there is strong friction when sawing, it means that the free cutting area is large.
Adjustment method:
(1)Loosen the two bolts connecting the slide seat and the bed
(2)Adjust the parallelism with two locknuts that clamp the workbench bolts on the side, (the sliding workbench and the fixed workbench have a certain gap) tighten the vertical screws.
4.3.2 Adjustment of the guide device on the fixed worktable relative to the saw blade
The left side of the saw blade should have the same parallelism difference. In order to check the adjustment, install the largest saw blade and correct the side elevation by using the parallel guide device. If the guide device is adjusted well, it depends on the free cutting in the diameter direction of the saw blade. , Use a 1-meter-long software to cut freely, and the test piece should not exceed 0.15mm.
Adjustment method:
(1)Loosen the outer nut of the two bolts holding the rod
(2)Adjust and tighten 2 lock nuts
(3)Fix it on the machine body with a nut.
4.3.3 Vertical angle cutting adjustment
The horizontal backing board of the sliding table is used for sawing the vertical angle. To adjust it correctly, take a piece of wood and cut 2 vertical planes. Use a square or feeler ruler to measure the length of 0.24mm at 500mm.
Adjustment method:
(1)Loosen the handle under the outer end of the lateral baffle
(2)Rotate the black star handle on the side
(3)When the school team is qualified, tighten all bolts.
4.3.4 Height adjustment of sliding table relative to fixed table
The sliding workbench is 0.3mm higher than the fixed workbench to avoid mutual friction when pushing the wood. If there is an abnormal situation, the fixed workbench should be adjusted and adjusted by the four corner support bolts of the distributed workbench.
Adjustment method:
- Lift the workbench: loosen the lower nut and tighten the
upper nut
(2)Workbench down: loosen the upper nut
(3)Check and adjust the parallel guide mechanism.
4.3.5Adjustment of the stability of the sliding table
Nylon rollers are installed on both sides of the slide, and the cylindrical surface of the roller rolls on the bottom plane of the slide seat to prevent possible swing and bumps during the movement of the movable table to make it stable. Roll along the guide to ensure the normal cutting of the machine tool. Stability and accuracy.
4.3.6.Parallel adjustment of the main saw blade and the auxiliary saw blade
The secondary saw blade is not parallel to the main saw blade, and there will be burrs or steps on the cutting surface of the sawing veneer board, so adjust it. Twist the auxiliary saw by hand to support the outer hexagon of the front side, so that the auxiliary saw can be moved inward or outward to be parallel to the main saw blade.
Leave a Reply
You must be logged in to post a comment.